3. 1. DEFINING TEAM GOALS
Without firmly established and effectively relayed goals and objectives, a team is unlikely to produce anything of consequence. One of the first requirements of any successful project team is to define goals and objectives which will provide the team with a mission statement and specific strategies by which it can realize the mission.
Some goals are often shaped by external organizations that run events and competitions that the team is interested in entering. In the design stage, these and other goals are usually outlined by student team leaders and experienced team members in collaboration with faculty advisors.
Initial team goals and objectives are usually quite broad in scope and ambition. As the team progresses, initial goals must be revisited to ensure compatibility with resources and time constraints and to flesh out details for deliverables in later phases. Team leaders and advisors must treat goals and objectives dynamically, revisiting and adapting them as required. Implausible goals can be demoralizing to an organization; goals that are too flexible are not particularly useful either as then team members may spend time on interesting matters which are not related to important but unstated goals. For example a lot of effort may go into a “cool” feature, but some fundamental property such as reliability may suffer.
Common broad goals for teams are:
- Meeting External Rules and Regulations:
A seemingly obvious goal, it is nevertheless easy to gloss over—and, if ignored, it can jeopardize all of the team’s efforts. For competition teams, this includes understanding and ensuring compliance with the competition’s rules and objectives. For non-competition teams with external deliverables (e.g., submission of results to an academic conference or journal), understanding external constraints is just as important. - Achieving Success:
Most student project teams are geared toward successful completion of main objectives. For competition teams, this can be defined as performing well in a student team competition. In non-competition teams, however, it is still helpful to have an agreed-upon benchmark that defines satisfactory completion of the task at hand. Without such a goal, it may be difficult to know when the project has been completed. Competitive teams should not think that "success" equals "winning." Although teams with a long history of winning (e.g., Cornell’s FSAE and RoboCup teams) may be justified in claiming victory as the ultimate goal, newer teams (e.g. Baja SAE) might be better served by less lofty ambitions in early years. Many new FSAE teams, for example, look to complete all events successfully and compete for rookie team awards—two goals that are themselves difficult to realize. - Avoiding Failure:
Part of achieving success is avoiding common or recurring causes of failure. It is perfectly reasonable for all teams to list not only what they would like to accomplish but also what they would like to avoid. - Innovation and Learning:
Stressing learning and innovation in a student project team can keep team members motivated and build new knowledge for later teams to build upon. However, the return on investment in fostering innovation is not always immediate. At times, learning and innovation directly conflict with short-term goals and deliverables. Balancing success and innovation can be difficult. - Fun:
Project teams are largely volunteer efforts. Even in cases where course credit is offered for team participation, the number of hours spent by team members usually exceeds normal credit hour requirements. Given this, the team should engage students not only intellectually but also socially. A fun atmosphere increases team morale and cohesion, builds a support structure for various personal and professional challenges, and creates a virtuous circle through which participation breeds more participation.
Making Goals Explicit
Once your team has defined its general goals, you must define achievable sub-goals. Goals should be specific, measurable, attainable, and tangible.
- Specific:
General goals such as a fast car are good overarching principles, but specific goals as 0-60 mph in 3.8 seconds are more likely to guide action. By reducing general goals to more specific ones (e.g., defining in greater detail what will be done by whom and when) your goals will be more effective in guiding team performance. - Measurable:
By making goals more specific, you make it possible to define metrics for success. - Attainable:
Goals that are too hard to accomplish or excessively aggressive are not necessarily helpful; repeated failures to meet goals can be disheartening and jeopardize future goals. - Tangible:
Goals with tangible outcomes and processes are more likely to be specific, measurable, and attainable. Intangible goals as “good design” are harder to define and measure and can be difficult to realize as a result.
3. 2. BRAINSTORMING
Brainstorming is a process of open-ended idea generation. Done correctly and at the right time, brainstorming can provide a team with more than enough potential avenues of investigation to consider. Done inappropriately, brainstorming can inadvertently shut out good ideas from the start. Done at the wrong time, it can simply confuse a team by injecting too much complexity into a process that can already appear chaotic to some participant. Yet, with instituted properly by team leaders and faculty advisors, brainstorming can spur a team to reach new, innovative levels of design and performance.
Brainstorming Essentials
Brainstorming should be:
- Unstructured:
Brainstorming should be as free of structure as possible at the beginning. The time to make sense of potential avenues of investigation comes at the close of brainstorming, definitely not at the beginning or during the idea stage. - Unconstrained by external influence:
Brainstorming should be conducted free of known constraints (e.g., competition rules, resource availability, etc.). Although feasibility is important to consider, the time to do so is later, after brainstorming is complete. - Democratic:
Good ideas can come from the least likely sources. Everyone from the newest to the most experienced team member should be encouraged to participate and share ideas openly. Again, the time to assign responsibility and duties is after brainstorming is complete.
Timing of Brainstorming
Brainstorming should happen very early in the design phase. In fact, it should be the first thing done in any design effort, even before people break up into subteams to investigate issues further. In some cases, it even happens before the team convenes—the Formula SAE team, for example, brainstorms ideas for the next car on the last day of competition and continues this discussion on the way home.
Brainstorming should be done when everyone is immersed in new ideas and relatively unencumbered by competing priorities. When real life interferes, the quality and quantity of ideas generated will suffer.
Brainstorming can be reinstituted as a problem solving tool at various points throughout the year but should not be done all the time. Especially when the team is coming up against an important deadline, brainstorming may not be the most efficient use of the team’s time.
Bringing Brainstorming to a Close
In any brainstorming session, ideas should be offered and recorded for future discussion. There should be no initial filtering of the list; any and all ideas should be offered as equal.
That said, all ideas are not created equal. Some are simply impossible. Others ignore the rules and regulations under which the team must operate. Some are impractical given human, time, and financial resources. Some are not very well thought out and easily bettered by competing ideas. However even the least practical ideas can have the germ of something useful in them and thus contribute to the brainstorming.
Once a complete list of ideas exists, the team must select and eliminate ideas. Brainstorming is closed by reintroducing certain elements of reality to the situation; many ideas are cancelled out by a simple appeal to the team’s goals, rules, resources, etc.
Some ideas will survive this first step of elimination but require considerable work to develop into something fruitful. This is where ideas gained through brainstorming should be subjected to the design review process to ensure that potentially valuable ideas are sufficiently developed.
3. 3. INTERNAL RESEARCH
Teams with long histories have a leg up on competing teams in that they can leverage past experience in their decisions. There are many ways a team can learn from past successes and failures.
In many instances, the tools and resources required to solve a problem are already known by the team in some form. However, tapping into this internal knowledge base is not easy, and in large organizations in particular, such collective amnesia can be a corresponding large problem. Team leaders and faculty advisors should encourage consistent team documentation and intra-team learning methods.
Team Documentation
In the course of its work, a team will usually generate a lot of artifacts and information valuable to its own experience and that of future teams. Documenting and storing this information is a complex process yet crucial to the continued improvement of the team.
Many teams have to produce formal documentation to enter a competition or to meet course credit requirements. These reports can be a valuable source of information.
Teams should realize, however, the limitations of this sort of information, especially as an exclusive source. Some engineers are simply not good writers and do not enjoy spending time to create proper documentation. Their reports can be sloppy and quickly dashed off to meet certain requirements; if so, their utility can be compromised.
It is also easily possible to become overwhelmed with too much information. The Cornell FSAE team, for example, has personal and technical reports dating back to the team’s early operations over 20 years ago. This database of 1500+ reports is a valuable resource, but finding particular details is like searching for the needle in the haystack. The team has dedicated time and resources to digitize this information and uses full-text searching on this database, but this is understandably a project that takes time and isn’t a short-term core goal for most team members, who are, in the end, engineers, not information scientists.
Even well-written reports are often not the best way to represent the full complexity of information. Formal reports are by definition edited documents, which suggests some information is necessarily left out to make the main points. Having access to the raw data behind the reports (e.g., test data, design notebooks, general notes) can often help fill in the gaps.
In addition, some processes and procedures aren’t easily documented. A report on welding, for example, will not simply transfer all required knowledge to the reader. Much knowledge and skill in welding is experientially based, and no report, no matter how well written, can faithfully replace hands-on experience with the art.
Learning from Team Members
Regardless of the team’s approach to documentation, a lot of key information exists as the experience of fellow team members. Sometimes the quickest and most effective means of discovering information can be a simple e-mail or phone call.
Team leaders and faculty advisors are an obvious first source of information. Team leaders are usually experienced with the team and its operations and, by acting as systems integrators may have relevant knowledge from other subteams’ work. Faculty advisors are often even more experienced and able to share information from their own knowledge, experiences and research; they can also refer team members to their colleagues for additional support and advice.
Despite this, it is sometimes difficult to solicit team leader and faculty advisor advice and guidance. New team members in particular may find it intimidating to reveal their lack of knowledge, and so they consult with the best available sources much later than they should. Team leaders and faculty advisors can help mitigate this by engaging team members in discussion and making themselves available to share information. This can be done through structured access opportunities such as office hours (in teams such as Solar Decathlon, team leaders also hold office hours regularly) and by leaders' and advisors' filling in gaps in their knowledge (e.g., asking questions and providing input in design reviews, providing lectures on core topics, etc.).
Although senior members and faculty advisors are valuable sources, good information also comes from listening to the experiences of newer team members. Many people have gained experience from other sources (e.g., hobbies, jobs) that can be very valuable. Teams should try to ensure that organizational hierarchy does not interfere with information flow; the quality of the information is more important than its source.
A team's alumni network can also be a valuable source of information. Many team alumni are happy to keep in touch with the team and its activities and are willing to provide background information on how and why they did what they did. In terms of team documentation, contacting the initial author if possible is usually the most efficient and correct way of resolving any issues with a particular report.
Learning by Doing
Sometimes, the best way to truly understand a given problem is to immerse oneself in it, even if others have already done so. This is particularly important for tacit, intangible sources of knowledge, such as the welding example noted above. No amount of research or consultation with experts will replace learning to perform a proper TIG weld by doing one.
Learning by doing is sometimes dismissed as a waste of time. If the team just reinvents the wheel, it can be. But in some instances it can be valuable to gain practical, experiential knowledge concerning a given problem, and providing the time and resources to do so is a worthy investment.
No matter how skilled the team members, leaders, and advisors are, inevitably the team cannot know everything internally and must seek advice, information, and feedback from external sources. .
3. 4. EXTERNAL RESEARCH
Learning from outside sources keeps the R&D process fresh and allows for fact-checking and verification early in the process. The potential for information overload must be appreciated, though; too much of a good thing is often confusing and overwhelming. Team leaders especially should read the following material on managing information acquisition and making sense of external sources as to assist general team members. Faculty leaders should guide leaders to narrow down the daunting amount of potential external sources. Too much information can be worse than no information at all if that information is not effectively integrated and used. By obtaining a grasp on the subject through internal sources first, team members can conduct pointed, effective searches through endless volumes of information.
Textbooks, Journal and Conference Articles, and Books
The library is a great place to start research. This should be obvious, but it is amazing how many team members fail to start here and thus miss out on potentially valuable sources of information.
One reason behind this is that the wealth of information out there is daunting; it’s hard to know where to begin. Course textbooks are often a good starting point because they are designed to be comprehensive investigations of a particular problem that reduce information to essential lessons. Most offer the reader additional resources to pursue investigation further.
Journal articles, conference papers, technical papers, and academic books are usually the next logical step. Again, there is a wealth of information available from these sources, often too much. It is impossible to be fully aware of all published sources on a given topic; information production is rapidly outpacing an individual’s ability to read it. Hitting key sources is essential. You can do this by noting references in publications—usually the key sources are cited by many articles and books, and lesser or more specialized resources are cited less. (This is not to say that you should ignore less-cited resources. If you do require a very esoteric piece of information, you can probably find it in a less-cited resource.)
Faculty advisors and university reference librarians can be excellent resources to help you focus your research and target especially valuable resources. Reference librarians are uniformly extremely helpful and knowledgeable sources. They are always very pleased to be asked to help find information and they are true experts, having a valuable master’s degree in how to find information. They have an intimate knowledge of helpful indices, interlibrary borrowing, etc. Often, project teams amass a small library of relevant literature that can narrow one’s search as well.
Expert Lectures and Consultation
Sometimes, the quickest way to integrate new information is to solicit the assistance of those already skilled in a particular field. A quick half-hour or hour lecture or consultation can be an effective way of learning new information and disseminating it to all team members.
Some teams are very adept at leveraging this. The Solar Decathlon team, for example, runs a weekly lecture series as part of course requirements, bringing in local and external experts to talk to the team about their areas of expertise. In addition, the team’s architectural design is vetted by panels of experts both here and externally, providing even more expert feedback and advice on the team’s work.
Popular, Trade, and Online Sources
Formal expert sources are not the only or necessarily even the best sources of information for some problems. Many problems are best solved by utilizing less academically rigorous publications like Web sites, popular magazines, trade magazines, blogs, etc. These sources can be valuable in researching industry contacts and soliciting the feedback and advice of lay practitioners in a field.
Due care must be taken with such sources, however. Many popular and trade magazines in particular are not peer-reviewed, whereas most academic journals are. In many cases information is inaccurate, exaggerated, or biased. This can lead to potential problems with partial or biased sources of information. Online sources in particular can be of varying and occasionally dubious levels of quality. Don’t ignore these sources, but do treat them with some caution and skepticism. They are probably best used in conjunction with more reliable or expert opinions. Also if an on-line source seems valuable it is best to download the information for the team’s use as many web sites disappear in a few months or years time.
Competitive Intelligence
Often, the best source of information regarding the dynamics of a particular student engineering team competition is competing teams.
Many engineering competitions are surprisingly cooperative affairs. Most team members are proud of their work and eager to discuss it with others. In the case of Formula SAE, team members attending competition can learn immense amounts of information by networking with fellow student competitors and studying alternative design concepts of the 130 attending schools.
Competitive intelligence is also increasingly done between competitions through online communication channels. Forums such as FSAE.com are excellent sources of information in general but probably most valuable in determining what other teams are up to.
Of course, this source is partial and certainly biased in its own right. Even in a highly cooperative environment, other teams are still competitors and are not likely to divulge information that will compromise their success or substantially increase your chance to best them in competition.
Reducing Information Complexity
Team leaders should watch out for team members getting bogged down with information overload and finding it difficult to cease research and move to development. Structures like design reviews** (have a link to Design Review homepage) help streamline the research process by setting key deadlines for the resolution of any research investigation.
3. 5. Dimensioning and Tolerancing Mechanical Parts
(Prepared by: Michael Hypes, Cornell University)
Preparation:
One of the most common problems for new designers is choosing dimensions that do not reflect the purpose of the part. Let us consider a nominal ¼” hole. Most new designers will simply put 0.25” or 0.250”, but in many cases this isn’t what was intended. Tapped holes, ones where you thread the hole, require a smaller hole be drilled, while clearance holes require a slightly larger hole be drilled. Press fits are generally the only ¼” hole that actually requires a ¼” drill. Once you know the intended uses of all your dimensions it is much easier to select the proper dimensions. A list of drill sizes for tapped and clearance holes is available online or in the machine shop.
Hole Type | Drill Size |
---|---|
¼”-20 Tapped | .2010 (#7) |
¼” Dowel Pin | .2500 (¼”) |
¼” Close Fit | .2570 (F) |
¼” Free Fit | .2660 (H) |
Dimensioning:
There are a few simple best practices which can help us dimension a working drawing:
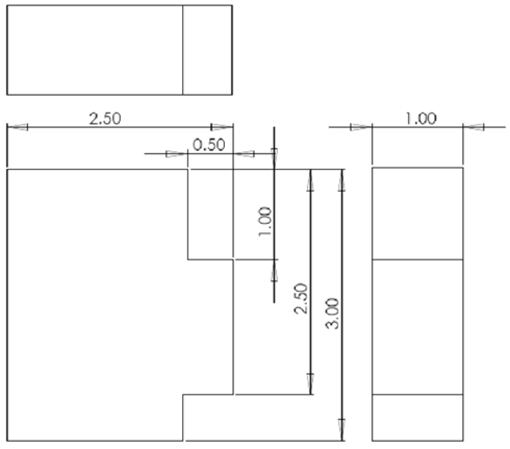
1. Place dimensions between views sharing dimensions, when possible
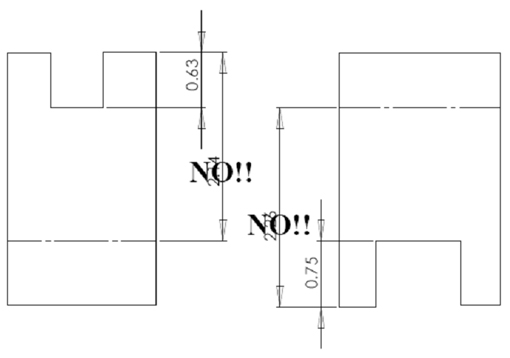
2. Do not dimension to hidden lines
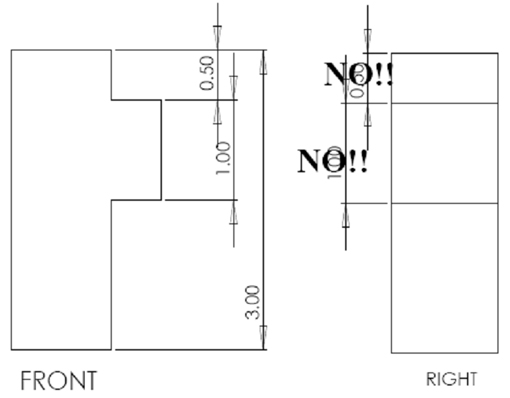
3. Dimension in a view that shows the geometric characteristics of the part
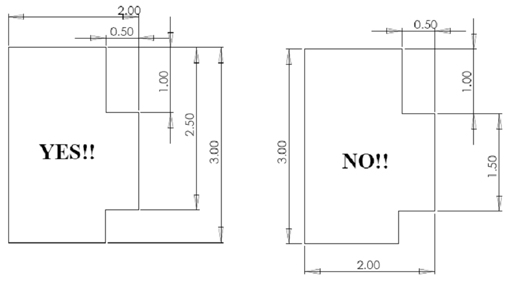
4. Group and organize Dimensions
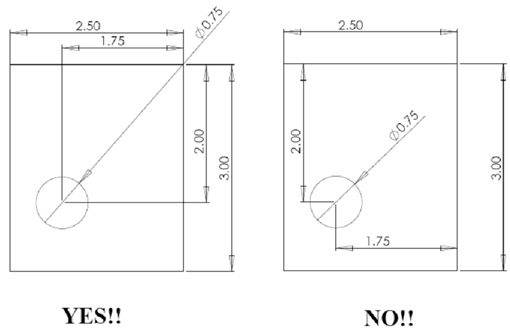
5. Do not place dimensions on the views
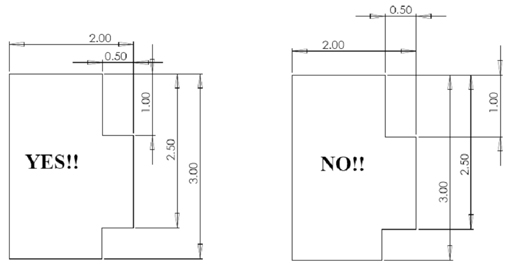
6. Dimension the shortest features first and move away from the view
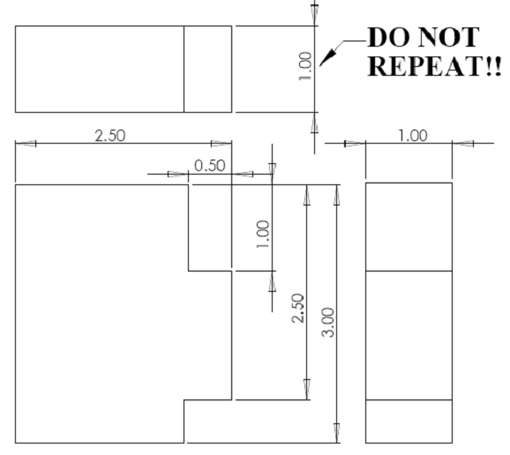
7. Do not repeat Dimensions
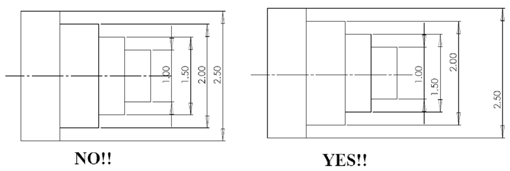
8. Stagger dimensions to make the part easier to read
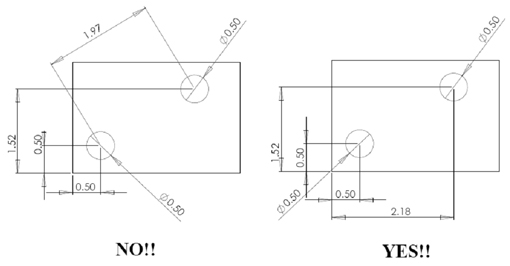
9. Dimension along a given coordinate system rather than using center to center dimensions
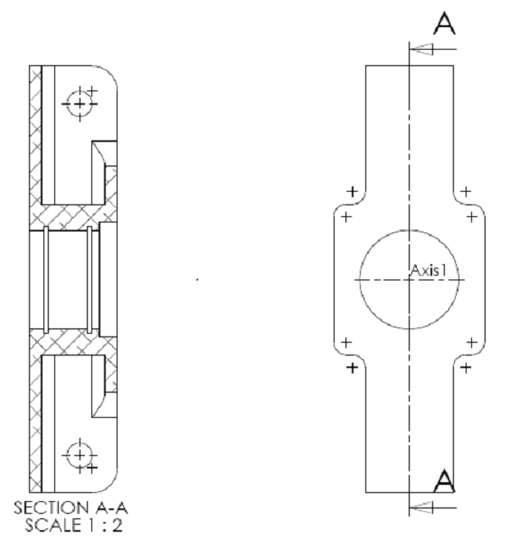
10. Use cut-away views to show internal features
Always use the same number of significant figures for all dimensions with the same tolerance (See Tolerancing on the following page…)
In addition to these best practices, it is helpful to consider how the part will be made. When using a mill, we generally define an origin either from one corner or a hole, if you dimension from different edges, it requires resetting the origin and can lead to alignment problems. When using a lathe, we generally define our coordinates from one face and the diameter of the part. In addition, as the lathe produces axisymmetric parts the most useful view is the view where the part appears as a rectangle.
Tolerancing:
When dimensioning parts, it’s very important to consider how precisely the part must be made. Many teams choose to have tolerance guidelines. An example of one of these conventions is 1.234 means ±0.0005”, 1.23 means ± 0.005”, 1.2 means ± 0.05”, etc. . . .
Using just one tolerance level may not be the best choice. Let us consider a jig plate. The distances and locations of the holes may need to be accurate to ± .0005”, but the external dimensions of the plate may be able to vary up to several inches. Having lower tolerances which do not affect the quality of the part can speed manufacture.
Also, you can use one-sided tolerances; these are common when there’s a maximum or minimum size. Let us consider making a pair of stacking boxes, one with an inner length of 3” and one with an outer length of 3” nominal, but each box will be made by a different person. To make sure that the boxes will fit together no matter what: the smaller box could be dimensioned to 2.995±.005 and the larger box to 3.005 ± .005. However, then we find that if everything is produced to specification we’ll end up with a gap of .010”. Instead to keep reasonable tolerances we can make the smaller box 3.000” +0/-.005 and the larger box 3.000”+.005/-0.
Finally, avoid accumulating tolerances. If you dimension off of one feature rather than dimensioning off of subsequent features it is possible to avoid large tolerances on the overall part. However, you should still keep important dimensions and always consider what dimensions on a part are critical. For example, if 3 holes need to be +/- .0005” from each other, they should be dimensioned off of each other, but the far edge should not be dimensioned off the 3rd hole if the overall part dimensions must be within some close tolerance.
Baja SAE History
The Cornell Baja team was founded in Fall 2003 and participates in SAE International’s Baja Series competition The project promotes the learning of theoretical concepts in a practical environment while meeting budget, scheduling and design requirements. The team is primarily made up of undergraduate students with a handful of graduate students. Four different colleges in the university are represented on our team, but the majority of our team members are engineers
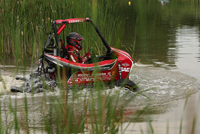
The Cornell Baja Team won its first international competition in school history. Cornell’s off-road racing vehicle outperformed 90 vehicles built by colleges and universities around the world at the 2010 Baja SAE Rochester World Challenge hosted by Rochester Institute of Technology in Rochester, New York from June 10-13, 2010.